Picking a Sustainable Insulation For Your Home
- mebryant213
- Aug 3, 2023
- 9 min read
Updated: Aug 4, 2023

Why should you consider improving the insulation of your home?
“The EPA estimates that homeowners can save an average of 11% on total energy costs by air sealing their homes and adding insulation in attics, floors over crawl spaces, and accessible basement rim joists.”
In 2021 the U.S. Energy Information Administration reported the average annual electricity consumption for a U.S. residential utility customer was 10,632 kilowatt hours (kWh), or 886 kWh per month. The average price per KWH was 13.66 cents per KWH bringing the average monthly electric bill for US homeowners to $121.01.
Using these figures, increasing the insulation of a home would save the owner on average $13.31 a month or $159.72 a year. Remember though, these are just averages. Depending on the current insulation in your home the total savings could be much greater.
In addition to the monthly utility savings, under the Energy Efficient Home Improvement Credit through 2032 homeowners who complete insulation projects can claim 30% of the total project cost (up to a maximum total credit of $1,200) as a tax credit when filing their taxes.
Picking a Sustainable Insulation
While much of the grid is still fueled by non-renewable sources, the energy savings generated by improved insulation in buildings equates to reduced carbon emissions and is environmentally beneficial. The environmental impacts of insulation go beyond just the energy savings generated though. Two important factors to consider when assessing the sustainability of insulation are embodied carbon and toxicity.
Embodied Carbon
Embodied carbon is the total carbon emissions generated throughout the materials lifespan. This includes ingredient extraction, manufacturing, transportation, installation, maintenance, and disposal. You’ll see this figure a lot as we compare building materials as it helps to better put into perspective the Global Warming Potential of each type.
Toxicity
Unfortunately many building materials on the market today are made using toxic ingredients. Exposure to these toxins can present themselves to those in the building at various times such as installation, when heated, gradually with usage, or when disturbed at the time of disposal. It’s important to understand the risks associated with each material type so they can be more safely managed. Since few of the most popular insulation options are completely free of some toxin or another we will look at both the advantages and disadvantages of each material type.
Before we move into the carbon footprint and toxicity of common insulation materials, let’s quickly review the common types of insulation for homes.
Common Types of Insulation for Homes
There are several common types of insulation for wooden framed homes- blown in, insulation blankets also called rolls or batts, spray foam insulation, and foam board insulation. Each type is best suited to different parts of the home and are often multiple types are combined to provide maximum thermal resistance.
Blown In

Best In- enclosed walls or hard to reach areas, unfinished attics floors
Blankets/ Batts/ Rolls
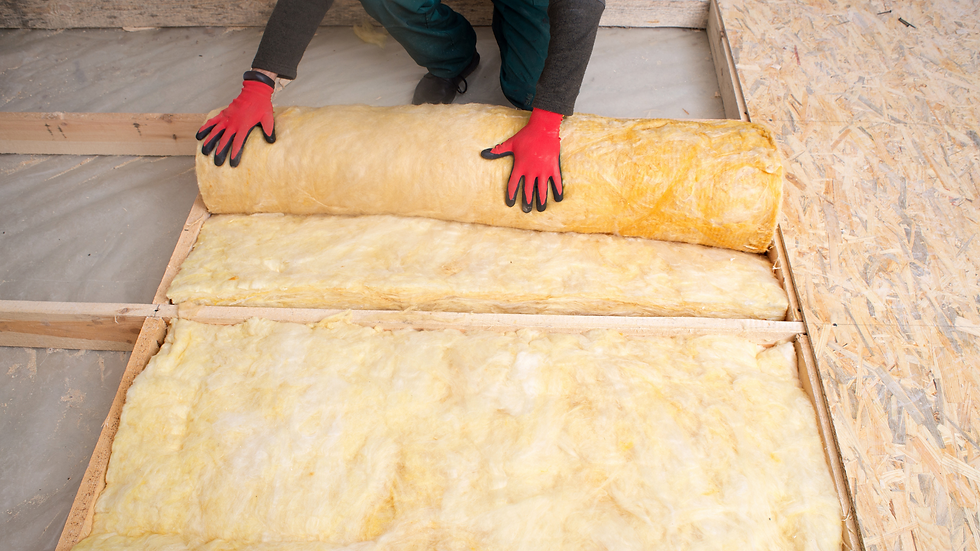
Best In- between studs in non- enclosed walls, floors and ceilings
Spray Foam

Best In- enclosed walls or hard to reach areas, unfinished attic floors
Foam Board

Best In- installed under siding, open wall studs, floors and ceilings, unvented low slope roofs
Carbon Footprint of Common Types of Insulation Materials
These figures were derived estimating an average home’s square footage of 2,105 square feet, insulated to the level needed to achieve an R-value of 15. When it comes to a products carbon footprint, the lower the number the better, as it means fewer carbon emissions are generated throughout the products lifecycle. A negative carbon footprint means the product actually removes more carbon from the air throughout it's lifecycle than it produces. A negative carbon footprint is most typical of plant materials as they filter CO2 out of the air through photosynthesis.
Blown In/Loose Fill-
Cellulose (-547) kg CO₂e
Sheep Wool 397 kg CO₂e
Fiberglass 516 kg CO₂e
Mineralwool 804 kg CO₂e
Insulation Blankets/Batts:
Cellulose (-919) kg CO₂e
Hempwool (-280) kg CO₂e
Fiberglass 343 kg CO₂e
Sheep Wool 517 kg CO₂e
Mineral Wool 873 kg CO₂e
Cotton 2618 kg CO₂e *Figure is based on virgin cotton but most insulation is made from recycled materials such as denim.
Spray Foam:
Polyurethane 2143 kg CO₂e
Polystyrene 2500 kg CO₂e
Foam Board:
Cork Board (-3,519) kg CO₂e
Mineral Wool Board 1715 kg CO₂e
Polyisocyanurate 2110 kg CO₂e
Polyurethane 2143 kg CO₂e *Based on spray foam polyurethane but footprint of foam board would be similar.
Polystyrene-
EPS 2461 kg CO₂e
XPS 2527 kg CO₂e
The carbon footprint estimates above give us a pretty good idea of which insulation materials we should be most highly considering in terms of sustainability but we also need to look further into the materials composition to better understand the products full environmental impacts and whether it presents any toxicity concerns. For example, fiberglass rated lower than sheep wool in terms of it's carbon footprint but as you will learn in the following section has a much higher level of toxicity concerns.
Advantages and Disadvantage of each insulation material type
Cellulose

Cellulose insulation is made from plant fibers derived from recycled paper.
Advantages
R Value of 3.5 per inch
Uses up to 85% recycled materials
Uses less energy to manufacture than other types of insulation
Itch free to the touch
Disadvantages
Some cellulose insulation is treated with borates (fire retardants)
Some inks in newspaper used may contain toxins
Newspaper is a dying industry meaning the supply of the materials used to generate this type of insulation will decrease over the coming years
Can lose R value as the insulation settles over time
Creates a lot of dust during installation
Absorbs moisture easily
Requires a vapor barrier
Fiberglass

Fiberglass is made using molten glass that is spun or blown into very fine glass fibers.
Advantages
Most manufacturers use 40-60% recycled glass content
Not flammable
Low dust levels during installation
Moisture resistant
Insects don’t eat fiberglass
Disadvantages
Lowest R Value of 2.5 per inch
Protective gear must be worn when installing fiberglass insulation as it causes irritation to skin if touched and lungs if inhaled
Some studies have linked fiberglass insulation to lung disease and cancer
Many fiberglass insulation products use formaldehyde to bind the glass fibers together
Manufacturing of fiberglass insulation is energy intensive
Requires a vapor barrier
Mineral (rock or slag) wool

There are two different types of mineral wool- rock and slag.
Rock wool is a synthetic material that contains natural rock minerals such as basalt or diabase.
Slag wool is a synthetic material made using the waste matter that forms on the surface of molten metal, referred to as slag.
Advantages
R Value of 4 per inch
Sound deadening properties
Contains around 70% recycled material
Moisture resistant
Fire resistant
Disadvantage
More Expensive than other types of insulation materials
Many mineral wool insulation products use formaldehyde to bind the the fibers together
Protective gear must be worn when installing mineral wool insulation as it causes irritation to skin if touched and lungs if inhaled
Mineral wool is very dense which makes it heavy and more difficult to install
Natural Fibers
Sheep's wool, Recycled denim cotton , and Hempcrete insulation
Insulation that is made using natural fibers such as cotton, sheep's wool, and hemp. Straw can also be used as insulation but allowance under building code varies from state to state so I’m not going to discuss it here.
Advantages
Comprised of natural, renewable materials
Plant based natural fibers tend to have a negative carbon footprint because they store more carbon over their lifecycle than is released through their usage
No protective clothing or equipment is required to handle or install it
Provides good sound dampening
Produce fewer air contaminants than many other types of insulation which leads to better indoor air quality in the home
Disadvantages
Some are chemically treated to make them fire retardant
Can attract pest
Can absorb moisture
Corkboard

Corkboard is made from harvesting the bark layer of the Quercus Suber, commonly called the Cork Oak tree.
Advantages
Long lasting
High level of dimensional stability
R value of 4 per inch
Hypoallergenic and free from any domestic toxins
Mold and mildew resistant
Thermal resistance does not decrease over time
Sound deadening properties
Naturally fire resistant
Disadvantages
More expensive than foam insulation
Cork can only be grown in certain parts of the world
Polyisocyanurate

Polyisocyanurate insulation also known as Polyiso is a rigid closed cell foam that is available in liquid, sprayed foam, and rigid foam board.
Advantages
R value of 6.2 per inch for foil faced polyiso foam board
High level of dimensional stability
Fire resistant
Disadvantages
Over time the R-value of Polyiso insulation can decrease due to some of the low-conductivity gas escaping and being replaced with air. This phenomenon is known as thermal drift
Made with methylene diphenyl diisocyanate (MDI) which is an allergen and sensitizer. People sensitive to MDI may have dangerous systemic reactions to extremely small exposures, including respiratory failure. Exposure to uncured MDI is greatest with spray foam applications
If caught on fire Polyiso releases a considerably higher level of toxins than other insulating materials
Foil faced Polyiso is vapor impermeable which can lead to excess moisture levels
Polyurethane

Polyurethane insulation is made of plastic that is created through a chemical reaction of polyols and isocyanates. It can be either rigid or flexible.
Advantages
R value 6.5 per inch
High level of dimensional stability
Moisture resistant
Fire resistant
Disadvantages
Carbon dioxide is used as a blowing agent to create a soft, comfortable feel. The more blowing agent used, the softer the resulting foam
In rigid foams, gasses are trapped in the closed cells of the foam to optimize insulation capacity. Over time these products can off-gas these often toxic fumes into the building
Spray applications generate uncured isocyanate vapors and dust which are hazardous. Even after cured these toxic chemicals can be released through insulation disturbances that create dust, heat generating processes near or on foam insulation, and fires
Over time the R-value of Polyurethane Insulation drops as the gas escapes the cells
Polystyrene
Polystyrene (PS) is a plastic made from the monomers of the hydrocarbon styrene. The two most popular types for insulation are Expanded Polystyrene(EPS Foam) and Extruded Polystyrene(XPS).

EPS is made using beads of foam in a mold. Heat or steam is applied to the beads which causes them to expand and fuse together. The board that is created is open celled.
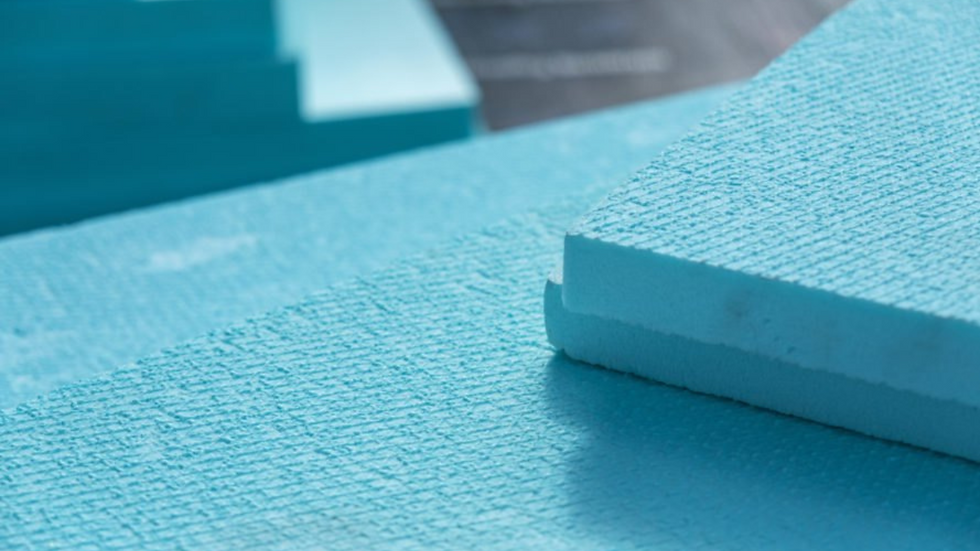
XPS is made using the process of extrusion which results in a closed cell structure with a smooth skin on the top and bottom on the insulation board.
EPS
Advantages
Cheaper than XPS
Lightweight
Moisture resistant
Mold and mildew resistant
Disadvantages
Lower R Value than XPS of 4 per inch
More fragile than XPS and susceptible to damage during install
Styrene is commercially manufactured from petroleum
Poor barrier to oxygen and water vapor
Low melting point
Incompatible with most electrical wiring. The protective plastic coating used on most common electrical wiring will erode prematurely if it comes into contact with the foam insulation which could lead to fires
Since the board is moisture resistant any moisture trapped in the wall will remain in the wall without a way to be vented away
XPS
Advantages
Higher R value than EPS of 4.7 per inch
Higher compressive strength than EPS
More durable and resistant to damage during install
Mold and mildew resistant
Disadvantages
More expensive than EPS
Styrene is commercially manufactured from petroleum
Poor barrier to oxygen and water vapor
Low melting point
Incompatible with most electrical wiring. The protective plastic coating used on most common electrical wiring will erode prematurely if it comes into contact with the foam insulation which could lead to fires
Since the board is moisture resistant any moisture trapped in the wall will remain in the wall without a way to be vented away
Final Thoughts
After reviewing both the carbon footprints and advantages and disadvantages of the various material types for sustainability I would select insulation made of natural fibers for blown in and blanket insulation and cork for board insulation. These options beat out cellulose for me because while the carbon footprint of cellulose is great the potential toxins from the inks and fire retardants are troubling. I would say it is still certainly a much better option than fiberglass or any of the poly insulation options, however.
With what you now know, which type of insulation what you choose for your home? Let me know in the comments.
Sources:
“2023 Blown-in Insulation Cost: Cellulose, Fiberglass, & Rockwool.” HomeGuide, homeguide.com/costs/blown-in-insulation-cost. Accessed 3 Aug. 2023.
“Best Home Insulation Boards.” InsulationGo LTD, insulationgo.co.uk/blog/best-insulation-board/. Accessed 3 Aug. 2023.
Carey, Sarah. “3 Ways to Insulate Siding and Reduce Home Energy Loss.” Progressive Foam Technologies, 30 Apr. 2020, www.progressivefoam.com/insulate-siding-reduce-home-energy-loss/.
Carey, Sarah. “What Is Thermal Bridging, and How to Stop It in a Home.” Progressive Foam Technologies, 8 Apr. 2020, www.progressivefoam.com/thermal-bridging-and-how-to-stop-it/.
“Cork Insulation Board – 10 Pros and Cons.” CorkSol, 15 Sept. 2022, corksoluk.com/latest-news/cork-insulation-board-10-pros-and-cons/.
“Fiberglass Insulation Pros and Cons.” Reliable Heating & Air, reliableair.com/blog/fiberglass-insulation-pros-and-cons. Accessed 3 Aug. 2023.
“Frequently Asked Questions (Faqs) - U.S. Energy Information Administration (EIA).” Frequently Asked Questions (FAQs) - U.S. Energy Information Administration (EIA), www.eia.gov/tools/faqs/faq.php?id=97&t=3. Accessed 3 Aug. 2023.
Green Insulation Group. “Pros and Cons of EPS and XPS.” Green Insulation Group, 2 Mar. 2023, greeninsulationgroup.com/pros-and-cons-of-eps-and-xps/.
“Havelock Wool Insulation – Sheep Wool Insulation for Buildings.” EcoBuilding Products, eco-buildingproducts.com/product/havelock-wool-insulation-sheep-wool-insulation/. Accessed 3 Aug. 2023.
“Hempwool: Hemp Wool Insulation.” Hempitecture Inc., www.hempitecture.com/hempwool. Accessed 3 Aug. 2023.
“Methodology for Estimated Energy Savings from Cost-Effective Air Sealing and Insulating.” ENERGY STAR, www.energystar.gov/saveathome/seal_insulate/methodology. Accessed 3 Aug. 2023.
Methylene Diphenyl Diisocyanate (MDI) Action Plan - US EPA, www.epa.gov/sites/default/files/2015-09/documents/mdi.pdf. Accessed 3 Aug. 2023.
“Mineral Wool Insulation Pros and Cons .” Solar365, www.solar365.com/green-homes/insulation/mineral-wool-insulation-pros-cons. Accessed 3 Aug. 2023.
Mordasky, Tom. “Open Cell vs Closed Cell Foam: Which Should I Choose?” Tiger Foam Insulation, 11 Mar. 2023, tigerfoam.com/sprayfoaminsulation/open-cell-vs-closed-cell-foam-which-should-i-choose/.
“Potential Chemical Exposures from Spray Polyurethane Foam.” EPA, 2 Sept. 2020, archive.epa.gov/epa/saferchoice/potential-chemical-exposures-spray-polyurethane-foam.html.
Ringler, Amanda. “What Is the R-Value of Spray Foam Insulation?” Spray Foam Insulation Contractor, 8 Jan. 2020, www.retrofoamofmichigan.com/blog/r-value-of-spray-foam-insulation.
“Types of Insulation.” Energy.Gov, www.energy.gov/energysaver/types-insulation. Accessed 3 Aug. 2023.
“U.S. Energy Information Administration - EIA - Independent Statistics and Analysis.” Electric Sales, Revenue, and Average Price - Energy Information Administration, www.eia.gov/electricity/sales_revenue_price/. Accessed 3 Aug. 2023.
“What Is the R-Value of Foam Board Insulation? (With Chart).” Attainable Home, 27 June 2022, www.attainablehome.com/what-is-the-r-value-of-foam-board-insulation/.
Comments